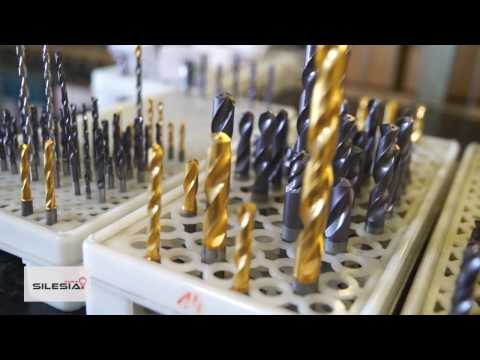
Zawartość

Wiertło zaczyna się od pręta wykonanego z wytrzymałego stopu stali. Taki trzon jest cylindryczny z gładkimi końcami i ogólnie ma tę samą średnicę co gotowe wiertło. Najpierw jeden z płaskich końców należy przekształcić w lekko nachyloną stożkową końcówkę. Aby to osiągnąć, w pełni zautomatyzowana maszyna chwyta pręt i obraca go szybko (ponad 1000 obrotów na minutę) wokół własnej osi (Rysunek 1). W międzyczasie maszyna obniża specjalne stacjonarne ostrze tak, aby dotykało krawędzi stalowego pręta pod pewnym kątem. Obracanie przedmiotu powoduje, że ostrze stopniowo dociera do końca wiertła, aż na końcu pozostaje tylko jeden stożek.
Porada

Wykonywanie spiralnych rowków

Maszyna przestaje obracać pręt i przesuwa go do pozycji cięcia śrubowych rowków wiertła. Tutaj cienka piła tarczowa (zwykle wykonana z ceramiki, sztucznego diamentu lub innego twardego związku) umieszczona ukośnie w stosunku do pręta i tnie go mniej niż milimetr w kierunku środka. Gdy to się dzieje, piła powoli porusza się równolegle do chwytu, gdy jest powoli obracana przez maszynę, co skutkuje gładkim spiralnym kanałem wzdłuż długości wiertła (Rysunek 2). Gdy piła dotrze do końca trzpienia, maszyna przestawia piłę od przodu, aby wyciąć drugi rowek w wiertarce.
Powłoka tytanowa
Aby wiertło było trwalsze, producent nakłada na całą jego powierzchnię cienką warstwę azotku tytanu (TiN). Azotek tytanu jest najczęściej nakładany w procesie zwanym „fizycznym osadzaniem z fazy gazowej” (DFV). W tym procesie wiertło jest umieszczane w komorze próżniowej z litym azotkiem tytanu. Gdy związek jest ogrzewany w środowisku bardzo niskiego ciśnienia (to znaczy w próżni), „sublimuje” (przechodząc ze stanu stałego bezpośrednio do stanu gazowego).
Jednocześnie gaz ten powoli osiada na powierzchni wiertła, jedna cząsteczka na raz, aż całe jego ciało zostanie pokryte cienką, trwałą warstwą.